How Can Rapid Die Casting and CNC Machining Accelerate Wearable Electronics Prototyping?
How Can Rapid Die Casting and CNC Machining Accelerate Wearable Electronics Prototyping?
Blog Article
Smartwatches, true wireless stereo (TWS) earbuds, and other wearable devices evolve on tight product cycles. Manufacturers must go from CAD drawings to physical prototypes within 7–10 days, ensuring components like zinc‑alloy housings feature ultra‑thin walls (down to 0.6–0.8 mm), mirror‑finished surfaces, and precision fit tolerances. Traditional machining alone struggles with such thin walls, and pure die casting without post‑processing cannot achieve the ±0.01 mm accuracy required for mating interfaces. Junyin’s integrated solution of die casting mold service capabilities addresses these pain points directly, shortening development cycles and improving yield.
How Does Junyin’s Workflow Ensure Fast Turnaround?
Upon receiving design specifications for a high‑end smartwatch housing, Junyin’s engineering team leverages UG NX for mold flow simulation and optimization. Within 48 hours, a precision die casting mold is finalized—incorporating thin‑wall fill channels, cooling fin geometry, and snap‑fit latch features. By day 3, the first zinc die‑cast samples are produced, resolving common fill issues in walls as thin as 0.6 mm. This rapid prototyping pace ensures that functional samples are ready for validation before the typical 7–10 day deadline, enabling design tweaks and early user feedback.
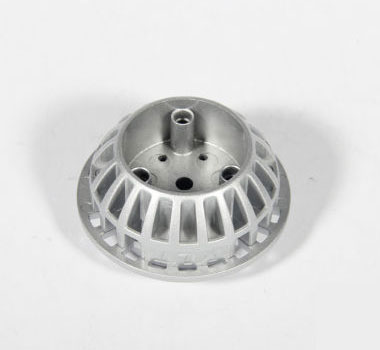
What Role Does CNC Machining Play in Achieving Precision?
After the initial die‑cast parts are validated, Junyin transitions to a high‑speed five‑axis CNC machining process. Critical features—such as the circular bezel outer round, touch sensor areas, and mounting posts—are machined to tolerances tighter than 0.003 mm. An automated tool‑setting system ensures consistent tool offsets, reducing setup time and eliminating human error. This dual approach—casting for complex shapes and milling for precision—delivers the ultra‑tight fits required by advanced wearable devices.
How Is Surface Quality and Durability Ensured?
Surface finish is critical for consumer appeal and functional performance. Junyin controls casting roughness to Ra 1.6 or better, reducing post‑processing time. After CNC machining, parts undergo physical vapor deposition (PVD) vacuum coating, achieving surface hardness above HV 200. This treatment not only enhances scratch resistance but also ensures corrosion protection. Optional processes—such as laser marking, anodizing, or powder coating—are available to meet decorative or regulatory requirements.
What Quality Standards Are Met Before Delivery?
Every prototype batch undergoes rigorous validation. Dimensional checks with coordinate measuring machines (CMM) verify that all critical tolerances, including roundness, flatness, and perpendicularity, fall within ±0.02 mm. Environmental tests—such as humidity cycling and salt spray exposure—confirm reliability in real‑world conditions. For clients in regulated industries, Junyin provides full documentation to IATF 16949 automotive standards or relevant IPC/JEDEC specifications.
Can Junyin Support Small‑Batch Production?
Beyond rapid prototyping, Junyin offers volume runs from 50 to 500 pieces with the same precision and surface quality. The seamless shift from prototype to pilot production avoids costly tool changes, ensuring consistency across batches. This model helps clients validate assembly processes, firmware integration, and user‑experience design before committing to mass production.
Why Is This Approach Preferred by Top Brands?
Leading wearable device brands—such as those developed by Apple and other innovators—prioritize speed, precision, and reliability. Junyin’s integrated die casting mold service coupled with advanced CNC machining manufacturer capabilities delivers on all fronts. Clients reduce development risks, cut time‑to‑market by up to two weeks, and maintain competitive advantage in fast‑paced consumer electronics segments.
How Does This Benefit Your Product Roadmap?
By compressing prototyping and pilot production timelines, product teams can iterate designs more frequently, incorporate user insights early, and align manufacturing readiness with marketing campaigns. The financial impact includes lower prototype scrap costs, reduced tooling expenditures, and minimized delays in certification processes—ultimately accelerating revenue generation.
Where Can You Learn More or Place an Order?
Ready to experience Junyin’s rapid die casting and precision machining for your next wearable electronics project? Visit their official page to explore services and request a quote:
For complementary insights on industrial design trends, check out Designboom, a leading online magazine covering product design innovations and manufacturing technologies.